316L Stainless Steel
316L Stainless Steel is the most widely used grade of stainless steel by the Pharmaceutical and Biotech Industries. All Eagle Stainless components are manufactured using 316L stainless Steel. Due to its unique properties, 316L stainless steel is highly resistant to corrosion.
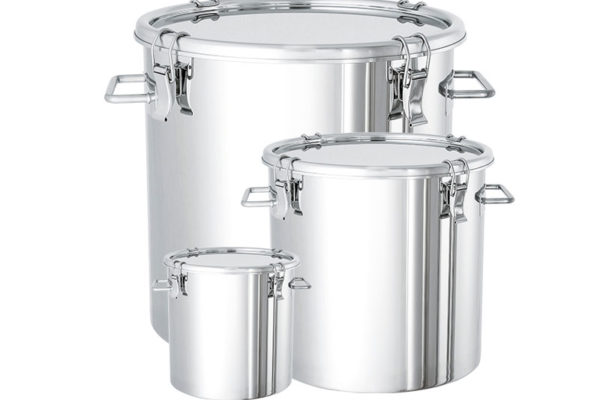
Among all the 300 series stainless steel, 316L contains lower carbon and it is austenitic with a structure that has a higher tensile strength. The process of high temperature and quick cooling during smelting makes 316L stainless steel Austenitic.
Specific percentages of chromium, nickel, molybdenum, iron, and lesser part of phosphorus, silicone, and sulfur are added together to create this alloy that makes 316L stainless steel corrosion resistant. Every batch of 316L stainless steel is provided with a mill certificate that shows the chemical composition that can be traced back to the mill. Eagle Stainless products are laser engraved with the mill certificate number for traceability.
The composition of 316L stainless steel contains molybdenum which imparts greater corrosion resistance than 304 stainless steel which does not contain molybdenum. 316L Stainless steel is used in the Pharmaceutical and Biotech Industry for processing equipment, storage tanks, pressure vessels, shipping vessels, tubing, valves, sanitary fittings as well as vessels for stability testing.
316L stainless steel, besides its properties of corrosion resistance and higher tensile strength, can achieve a surface finish of 10 Ra or lower by mechanical polishing. It could also be electropolished to reach a smoother curve under a microscope eliminating high peaks and valleys that can trap any impurities. Lastly it could be passivated to ASTM standard to remove contaminants and promote the formation of the passive film on a freshly electropolished or non-electropolished surface.
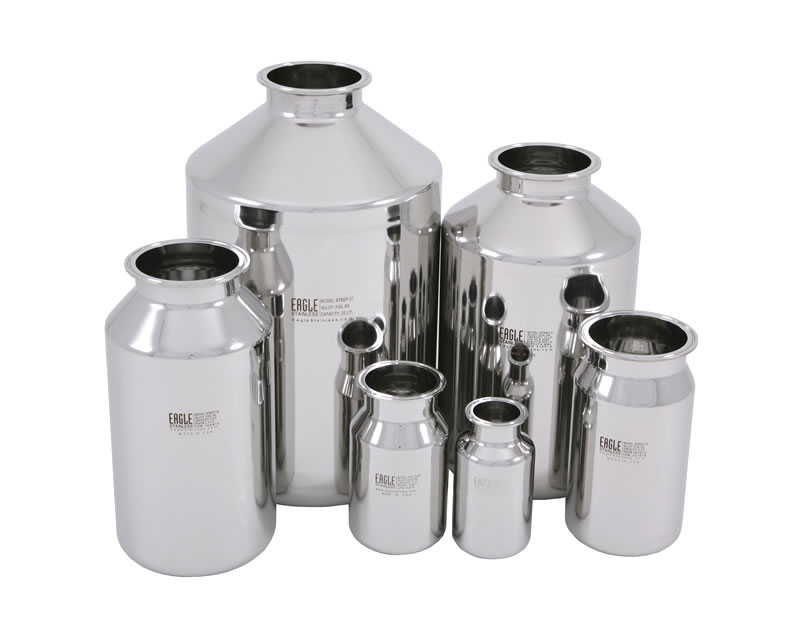
The FDA approves the use of 316L stainless steel as an industry standard for pharmaceutical manufacturing, specifically for its corrosion resistance, achievement of surface finish, cleanability, non reaction to most chemicals, tensile strength, and durability.